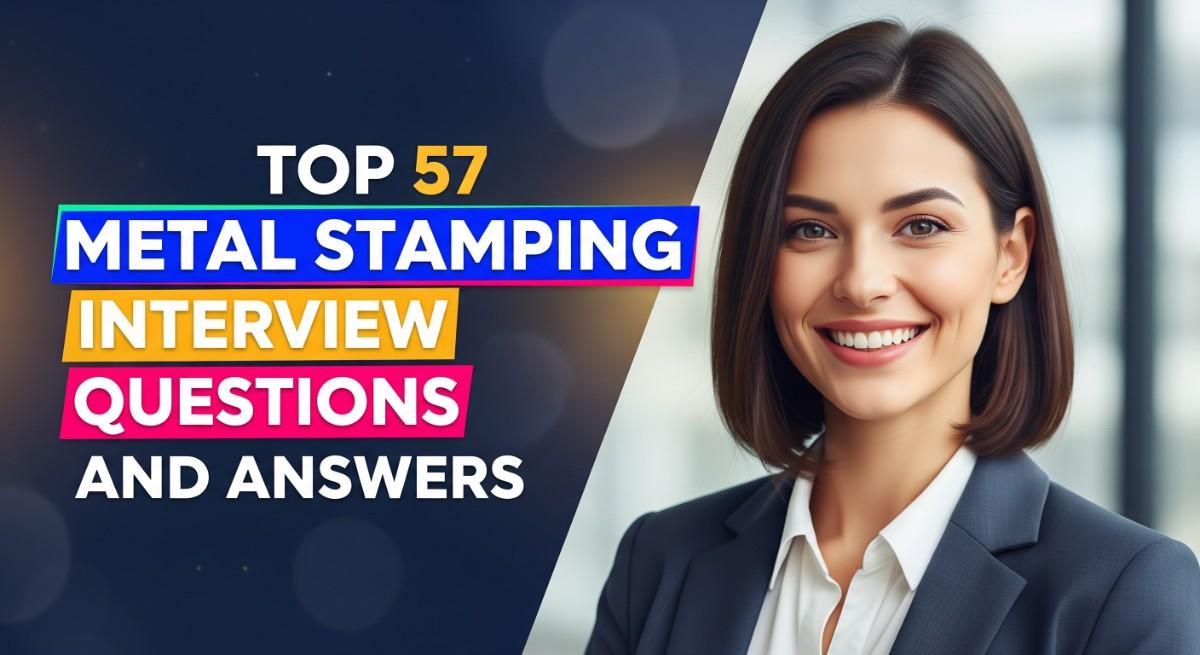
Preparing for a metal stamping interview requires a unique blend of technical knowledge and practical skills. This role is pivotal in the manufacturing industry, as metal stamping plays a crucial part in producing components for various applications, from automotive to electronics. Proper interview preparation is essential to stand out among candidates, showcasing your understanding of metal forming processes, machinery, and safety standards. In this comprehensive guide, we will cover common interview questions, key concepts to master, and effective strategies for demonstrating your expertise and problem-solving abilities. With the right preparation, you can confidently navigate the interview process and secure your place in this dynamic field.
What to Expect in a Metal stamping Interview
In a metal stamping interview, candidates can expect a mix of technical and behavioral questions. Typically, the interview may be conducted by a hiring manager, engineers, or HR representatives. The structure often begins with an overview of the candidate’s background followed by specific inquiries about metal stamping processes, machinery, and safety protocols. Practical assessments or problem-solving scenarios may also be included to evaluate hands-on skills. Candidates should be prepared to discuss past experiences, teamwork, and how they handle challenges in a manufacturing environment.
Metal stamping Interview Questions For Freshers
This set of Metal stamping interview questions is tailored for freshers, focusing on essential concepts in the field. Candidates should master fundamental topics such as materials, processes, and basic principles of metal stamping to demonstrate their readiness for entry-level positions.
1. What is metal stamping and how does it work?
Metal stamping is a manufacturing process that involves shaping metal sheets into desired forms using a die. The process usually includes cutting, bending, and piercing operations, where a punch creates the desired shape by forcing the metal sheet against a die. It is commonly used for producing parts in bulk with high precision and efficiency.
2. What materials are commonly used in metal stamping?
- Steel: Widely used for its strength and durability, especially in automotive parts.
- Aluminum: Lightweight and corrosion-resistant, often used in the aerospace industry.
- Copper: Known for its excellent conductivity, used in electrical components.
- Brass: Offers good corrosion resistance and is used in decorative items and fittings.
Choosing the right material is crucial as it affects the stamping process and the final product’s properties.
Build your resume in just 5 minutes with AI.
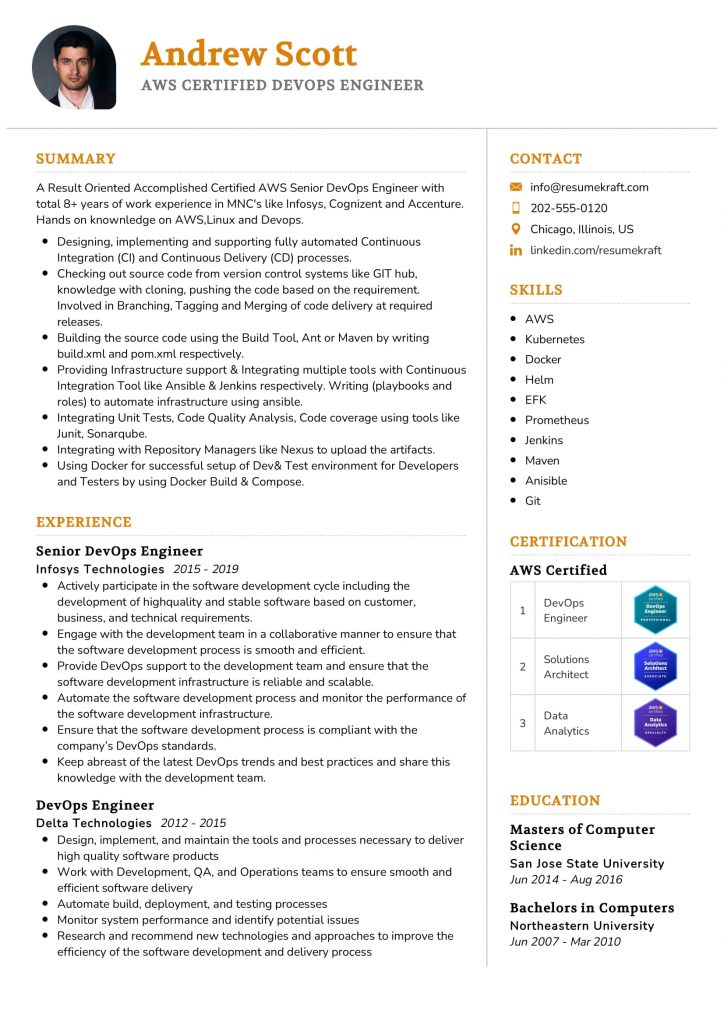
3. What are the main advantages of metal stamping?
- High Efficiency: Capable of producing large quantities of parts quickly.
- Cost-Effectiveness: Reduces waste and lowers production costs over large runs.
- Precision: Produces parts with tight tolerances and complex geometries.
- Versatility: Can be used on various materials and for multiple applications.
These advantages make metal stamping a preferred choice in many manufacturing sectors.
4. Can you explain the difference between progressive die and compound die?
- Progressive Die: This die performs multiple operations in a sequence as the metal moves through it. Ideal for high-volume production.
- Compound Die: Performs multiple operations simultaneously in one stroke, typically used for simpler parts.
Understanding these differences helps in selecting the right die for specific manufacturing needs.
5. What is the role of a punch and die in the stamping process?
The punch and die are critical components in the metal stamping process. The punch is a tool that cuts or shapes the metal, while the die serves as the counterpart that shapes the metal sheet into the desired form. Together, they ensure precise and accurate production of parts, maintaining quality and consistency.
6. What is the significance of tolerance in metal stamping?
Tolerance in metal stamping refers to the acceptable limits of variation in a part’s dimensions. It is crucial as it affects the fit and functionality of the stamped parts in their final assembly. Maintaining tight tolerances is essential for quality assurance, ensuring parts meet design specifications and perform effectively in their intended applications.
7. How do you determine the thickness of metal sheets for stamping?
The thickness of metal sheets for stamping is determined based on the application requirements and the properties of the material. Factors such as strength, weight considerations, and the complexity of the shapes being produced also play a role. Typically, manufacturers select thicknesses that balance performance with cost-effectiveness for the intended application.
8. What is blanking in metal stamping?
Blanking is the first operation in the metal stamping process where a flat sheet of metal is cut into a desired shape or blank using a punch and die. The blank is then used for further processing such as bending or forming. This operation is essential for creating parts that require specific dimensions and shapes.
9. What are some common defects in metal stamping?
- Scratches: Caused by dirt or debris on the die surface.
- Burrs: Sharp edges left on the part after cutting due to insufficient clearance.
- Wrinkling: Occurs when the material is not properly supported during forming.
- Dimensional Nonconformance: Parts that do not meet specified tolerances.
Identifying and addressing these defects is crucial for ensuring high-quality production.
10. What safety measures should be taken during the stamping process?
- Personal Protective Equipment (PPE): Always wear safety glasses, gloves, and steel-toed boots.
- Machine Safety: Ensure all guards and safety devices are in place before operation.
- Emergency Procedures: Familiarize yourself with emergency stops and procedures.
- Training: Operators should be adequately trained in machine operation and safety practices.
Implementing these safety measures helps prevent accidents and injuries in the workplace.
11. Can you explain the concept of die maintenance?
Die maintenance involves regular inspection, cleaning, and repair of stamping dies to ensure they operate efficiently and produce high-quality parts. Proper maintenance extends the lifespan of the dies, minimizes defects, and reduces downtime during production. It is essential for maintaining operational efficiency in a stamping facility.
12. What is the purpose of lubrication in metal stamping?
Lubrication in metal stamping reduces friction between the die and the metal, preventing wear and tear on the tools and improving the quality of the stamped parts. It also helps to cool the tools during operation, preventing overheating. Proper lubrication is essential for maintaining production efficiency and ensuring the longevity of the stamping equipment.
13. How do you select the right metal stamping process for a project?
- Material Type: Consider the properties of the material being used.
- Part Complexity: Assess the complexity of the design and the required tolerances.
- Production Volume: Determine if the project is for low or high volume production.
- Cost Constraints: Evaluate the budget available for tooling and production.
By analyzing these factors, one can select the most suitable stamping process to meet project requirements.
14. What is forming in metal stamping?
Forming in metal stamping refers to the process of shaping the metal into a specific configuration using a die without cutting it. This can include bending, stretching, and drawing operations. Forming is essential for creating parts with complex shapes and is often used after blanking to achieve the final design.
15. What advancements are currently being made in metal stamping technology?
- Automation: Increasing use of robotics for handling and processing materials.
- 3D Printing: Integration of additive manufacturing for complex part design.
- Smart Manufacturing: Implementation of IoT for real-time monitoring and efficiency optimization.
- Advanced Materials: Development of lightweight and high-strength materials for enhanced performance.
These advancements are transforming the metal stamping industry, leading to improved efficiency and capabilities.
These questions are tailored for freshers entering the metal stamping industry and cover essential concepts they should be familiar with.
16. What is metal stamping and how is it used in manufacturing?
Metal stamping is a manufacturing process that involves converting flat metal sheets into specific shapes using dies and stamping presses. It is widely used for producing parts in various industries, including automotive, aerospace, and electronics. The process can include operations such as blanking, bending, and piercing, allowing for high precision and high-volume production of metal components.
17. What are the different types of metal stamping processes?
- Blanking: This process involves cutting out a flat piece of metal from a larger sheet.
- Forming: This process shapes the metal using pressure to create bends or curves.
- Piercing: In this process, holes are created in the metal sheet.
- Embossing: This adds raised or recessed designs on the surface of the metal.
Each of these processes serves different purposes and can be combined to create complex parts efficiently.
18. What materials are commonly used in metal stamping?
Common materials used in metal stamping include:
- Steel: Often used for its strength and durability.
- Aluminum: Valued for its lightweight and corrosion resistance.
- Brass: Used for its excellent conductivity and aesthetic appeal.
- Stainless Steel: Preferred for its corrosion resistance and strength in harsh environments.
The choice of material depends on the application’s requirements, such as strength, weight, and resistance to environmental factors.
19. What safety precautions should be taken during metal stamping operations?
- Personal Protective Equipment (PPE): Always wear appropriate gear such as gloves, safety glasses, and steel-toed boots.
- Machine Safety: Ensure all safety guards are in place and that emergency stop buttons are functional.
- Training: Operators should be properly trained on machine operation and safety protocols.
- Work Area Maintenance: Keep the work area clean and free from hazards to prevent accidents.
Implementing these safety measures helps protect workers and minimizes the risk of accidents during operations.
20. How do you ensure quality control in metal stamping processes?
Quality control in metal stamping involves several practices:
- Regular Inspections: Conduct frequent inspections of parts during and after production to ensure they meet specifications.
- Use of Gauges: Utilize precision gauges and measuring instruments to check dimensions and tolerances.
- Process Monitoring: Track critical parameters such as temperature, pressure, and speed during the stamping process.
- Feedback Loops: Implement a system for feedback from operators to continuously improve processes.
By integrating these practices, manufacturers can maintain high standards of quality and reduce waste in production.
Metal stamping Intermediate Interview Questions
This section covers intermediate-level metal stamping interview questions that candidates should master. They should understand concepts such as material properties, tooling design, process parameters, and quality control techniques to succeed in practical applications and real-world scenarios.
21. What factors influence the choice of material for metal stamping?
Material selection for metal stamping is influenced by several factors, including:
- Mechanical Properties: Strength, ductility, and hardness are critical for determining how well a material can withstand the stamping process.
- Formability: The material’s ability to be shaped without cracking or deforming affects its suitability for stamping.
- Cost: The economic viability of the material in mass production scenarios must be considered.
- Corrosion Resistance: Depending on the application, materials may need to withstand harsh environments.
Choosing the right material ensures the final product meets performance and durability standards.
22. How do you determine the appropriate die design for a stamping operation?
Determining the appropriate die design involves several considerations:
- Part Geometry: The shape and complexity of the part dictate the die type (e.g., progressive, compound).
- Tolerance Requirements: The precision required for the stamped part influences the die design and manufacturing process.
- Material Thickness: Thicker materials may require more robust die designs to handle the stresses involved.
- Production Volume: High-volume runs may benefit from more intricate die designs for efficiency.
A well-thought-out die design can significantly enhance production efficiency and product quality.
23. What is the purpose of using lubricants in metal stamping?
Lubricants serve multiple purposes in metal stamping, including:
- Reducing Friction: Lubricants minimize wear on dies and the material, leading to longer tool life.
- Improving Surface Finish: They help achieve a smoother surface on the stamped parts.
- Preventing Galling: Lubricants can prevent material from sticking to the die, which can cause defects.
- Heat Dissipation: Lubricants can help dissipate heat generated during the stamping process, reducing the risk of thermal damage.
Overall, using the right lubricants can enhance product quality and operational efficiency.
24. Explain the concept of “springback” in metal stamping.
Springback refers to the tendency of a material to return to its original shape after being deformed during stamping. Key points include:
- Material Properties: Materials with high elasticity are more prone to springback.
- Die Design: Proper die design can help compensate for springback effects.
- Process Parameters: Adjustments in stamping pressure and speed can influence the degree of springback.
- Predictive Models: Engineers often use simulation software to predict and manage springback outcomes.
Understanding and managing springback is crucial for ensuring dimensional accuracy in stamped parts.
25. What are some common defects in stamped parts and their causes?
Common defects in stamped parts include:
- Wrinkling: Often caused by improper material feeding or insufficient blank holder pressure.
- Cracking: May occur due to excessive strain or using materials with poor ductility.
- Dimensional Inaccuracy: Can be a result of tool wear, improper die alignment, or incorrect process parameters.
- Surface Defects: These might arise from inadequate lubrication or contamination on the material surface.
Identifying and addressing these defects early can save costs and improve product quality.
26. How can you optimize the stamping process for efficiency?
Optimizing the stamping process involves several strategies:
- Tooling Design: Invest in high-quality, efficient tooling to reduce cycle times.
- Material Utilization: Maximize material usage to minimize waste and costs.
- Automation: Implement automation in feeding and unloading to speed up production.
- Process Monitoring: Use real-time monitoring systems to detect issues early and adjust parameters accordingly.
Through continuous improvement and monitoring, the stamping process can be made significantly more efficient.
27. What role does quality control play in metal stamping?
Quality control in metal stamping is vital for ensuring product consistency and reliability. Key aspects include:
- Inspection Techniques: Regular inspections and measurements help identify defects early.
- Statistical Process Control: Monitoring process variations can guide adjustments to maintain quality.
- Material Testing: Ensuring materials meet specified standards is crucial for performance.
- Feedback Loops: Implementing feedback systems allows for adjustments based on production data.
Effective quality control mechanisms lead to high-quality products and reduced rework costs.
28. Describe the difference between progressive and compound dies.
Progressive and compound dies serve different functions in stamping operations:
- Progressive Dies: These allow multiple operations to be performed in a single stroke, feeding the material through several stations to complete the part.
- Compound Dies: They perform two or more operations simultaneously in one stroke, typically cutting and forming the part in one step.
The choice between the two depends on the complexity of the part and production volume requirements.
29. What are some advancements in metal stamping technology?
Recent advancements in metal stamping technology include:
- High-Speed Presses: These enhance production rates and reduce cycle times.
- Advanced Materials: New materials, such as lightweight alloys, improve performance and efficiency.
- Simulation Software: Software tools allow for better die design and process optimization.
- Automation: Robotics and automation systems streamline operations and reduce labor costs.
Staying updated with these advancements can significantly improve manufacturing processes and product quality.
30. How do you troubleshoot a stamping operation that frequently produces defects?
Troubleshooting a defective stamping operation involves a systematic approach:
- Review Process Parameters: Check settings such as pressure, speed, and lubrication.
- Inspect Tooling: Examine dies for wear or damage that could affect part quality.
- Analyze Material: Ensure that the material used meets specifications and is appropriate for the design.
- Conduct Root Cause Analysis: Investigate potential causes of defects through data analysis and testing.
By addressing these areas, many defects can be mitigated or eliminated, improving overall production quality.
31. What safety measures should be implemented in a metal stamping operation?
Safety measures in metal stamping operations include:
- Machine Guards: Ensure that all machines have appropriate guards to protect operators from moving parts.
- Personal Protective Equipment (PPE): Employees should wear gloves, safety glasses, and steel-toed boots.
- Training: Regular safety training for all employees on machine operation and emergency procedures.
- Emergency Stops: All machines should be equipped with easily accessible emergency stop buttons.
Implementing these safety measures helps create a safer working environment and reduces the risk of accidents.
32. How does temperature affect the metal stamping process?
Temperature plays a crucial role in metal stamping, influencing several factors:
- Material Properties: Higher temperatures can increase ductility, making materials easier to form.
- Tool Wear: Elevated temperatures can lead to quicker wear of stamping tools, affecting their lifespan.
- Lubrication: The effectiveness of lubricants can change with temperature, impacting friction and surface finish.
- Springback: Material behavior related to springback can vary with temperature changes.
Understanding temperature effects is essential for optimizing the stamping process and achieving high-quality results.
33. What is the significance of blanking in the stamping process?
Blanking is a critical first step in the stamping process, involving cutting out flat shapes from a sheet of material. Its significance includes:
- Material Utilization: Efficient blanking maximizes the use of material, reducing waste.
- Part Preparation: It prepares the material for subsequent forming operations, ensuring accurate dimensions.
- Cost Efficiency: Effective blanking can lower production costs by minimizing scrap and optimizing cycle times.
- Quality Control: Proper blanking techniques ensure that the blanks meet required specifications, reducing downstream defects.
Overall, blanking is foundational to the stamping process and directly impacts product quality and cost-effectiveness.
These questions are designed for candidates with intermediate knowledge of metal stamping, focusing on practical applications, performance considerations, and industry best practices.
36. What are the key factors to consider when designing a metal stamping die?
When designing a metal stamping die, several key factors must be considered to ensure efficiency and effectiveness:
- Material Selection: The choice of material affects die longevity and performance; harder materials are often used for high-volume production.
- Part Geometry: The complexity of the part being stamped influences the die design, including the need for specialized features.
- Clearance: Proper clearance between the die and punch is essential to prevent excessive wear and ensure clean cuts.
- Production Volume: High-volume production may require robust, durable dies, while low-volume runs might use simpler designs.
Taking these factors into account can significantly enhance the quality and efficiency of the stamping process.
37. How do you troubleshoot common issues in metal stamping operations?
Troubleshooting metal stamping operations involves assessing several common issues, such as:
- Material Defects: Inspect raw materials for flaws that can cause problems during stamping.
- Die Wear: Regularly check dies for wear and tear, as worn dies can lead to poor part quality.
- Alignment Issues: Ensure that the die and punch are properly aligned to avoid misalignment errors during stamping.
- Inconsistent Pressure: Monitor stamping pressure to ensure it remains consistent throughout the production run.
By systematically addressing these areas, operators can quickly identify and resolve issues that may arise during the stamping process.
38. What are the benefits and drawbacks of using progressive dies in metal stamping?
Progressive dies offer several benefits and drawbacks in metal stamping processes:
- Benefits:
- Increased Efficiency: Progressive dies allow for multiple operations in a single stroke, reducing cycle time.
- Cost-Effectiveness: They are ideal for high-volume production, minimizing material waste and labor costs.
- Consistent Quality: Parts produced are more uniform due to the automation of the stamping process.
- Drawbacks:
- Higher Initial Costs: The upfront investment for designing and manufacturing progressive dies is significant.
- Complex Setup: Setting up progressive dies requires precision and expertise, making initial production runs challenging.
- Benefits:
Understanding these pros and cons helps manufacturers decide whether progressive dies are suitable for their specific production needs.
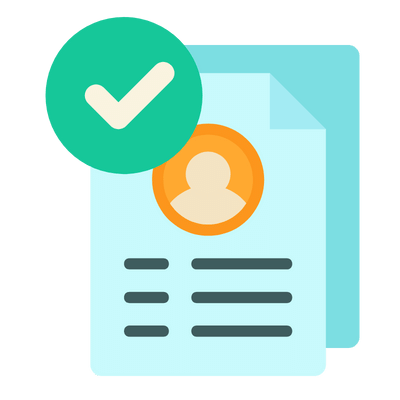
Build your resume in 5 minutes
Our resume builder is easy to use and will help you create a resume that is ATS-friendly and will stand out from the crowd.
39. Can you explain the role of lubrication in metal stamping operations?
Lubrication plays a critical role in metal stamping operations by:
- Reducing Friction: Proper lubrication minimizes friction between the die and the material, reducing wear and extending die life.
- Improving Surface Finish: Lubricants help achieve a better surface finish on stamped parts by preventing galling and scratches.
- Enhancing Material Flow: Lubrication aids in the smooth flow of material during the stamping process, reducing the likelihood of defects.
- Heat Dissipation: Lubricants can help dissipate heat generated during stamping, preventing overheating of dies and materials.
Overall, effective lubrication is essential for optimizing the performance and longevity of both dies and stamped parts.
40. What are common materials used in metal stamping, and how do their properties affect the stamping process?
Common materials used in metal stamping include:
- Steel: Offers high strength and durability, making it ideal for various applications. However, it may require more force during stamping due to its hardness.
- Aluminum: Lightweight and malleable, aluminum is easier to stamp but may require special considerations to avoid deformation.
- Copper: Known for its excellent conductivity, copper can be stamped into intricate shapes, but its softness can lead to wear on stamping dies.
- Brass: Combines the properties of copper and zinc, providing good machinability and corrosion resistance, but can be more expensive than other materials.
Understanding the properties of these materials is crucial for optimizing the stamping process and selecting the appropriate equipment and settings.
Metal stamping Interview Questions for Experienced
This set of Metal stamping interview questions for experienced professionals delves into advanced topics such as optimization techniques, scalability challenges, design patterns, and leadership in the industry. Candidates will be expected to demonstrate their expertise and strategic thinking in designing and improving metal stamping processes.
41. What are the key considerations for optimizing a metal stamping process?
Key considerations for optimizing a metal stamping process include material selection, die design, machine setup, and production speed. It’s essential to evaluate the material properties to ensure compatibility with the stamping process. Proper die design minimizes waste and improves part quality, while optimizing machine setup and production speed can significantly enhance overall efficiency and reduce cycle times.
42. Can you explain the role of tooling in metal stamping?
Tooling plays a critical role in metal stamping as it directly affects the accuracy and quality of the stamped parts. The design and fabrication of dies and punches are crucial for achieving precise dimensions and tolerances. Proper maintenance of tooling is also essential to prevent wear and tear, which can lead to defects and increased production costs.
43. How do you ensure scalability in a metal stamping operation?
- Assess Equipment Capability: Evaluate the current machinery and determine if it can handle increased production volumes or if additional equipment is needed.
- Process Standardization: Standardize processes to reduce variability and ensure consistent quality, which simplifies scaling up operations.
- Training and Development: Invest in training staff to handle higher volumes efficiently while maintaining quality standards.
By focusing on these areas, a metal stamping operation can effectively scale to meet increased demand without sacrificing quality.
44. What design patterns do you find most useful in metal stamping?
In metal stamping, design patterns such as modular design and concurrent engineering are particularly useful. Modular design allows for easier adjustments and replacements of specific components without redesigning the entire system. Concurrent engineering fosters collaboration between departments, enabling faster problem-solving and innovation during the design and production phases.
45. How do you approach leadership and mentoring in a technical team?
Effective leadership in a technical team involves fostering a collaborative environment, encouraging open communication, and providing opportunities for professional development. Mentoring team members through regular check-ins, offering constructive feedback, and sharing knowledge on best practices helps build a competent team. Establishing clear goals and celebrating achievements also motivates the team and enhances performance.
46. What are the common defects in metal stamping, and how can they be prevented?
- Wrinkling: Prevented by proper die design and material selection.
- Dimensional Inaccuracy: Can be addressed by regular calibration of machines and tools.
- Surface Defects: Ensured by maintaining clean tooling and optimizing lubrication.
Understanding these defects and their prevention techniques is crucial for maintaining high-quality production.
47. How do you analyze the cost-effectiveness of a metal stamping operation?
To analyze the cost-effectiveness of a metal stamping operation, consider factors like material costs, labor costs, overhead, and machine efficiency. Calculate the total cost of production and compare it to output quality and quantity. Utilizing techniques like value stream mapping can help identify areas for cost reduction while maintaining quality and throughput.
48. Describe a situation where you had to troubleshoot a complex stamping issue.
In a recent project, we faced issues with inconsistent part dimensions. I led a root cause analysis, which involved reviewing the die design, machine settings, and material properties. By adjusting the clearance in the die and recalibrating the machine, we were able to resolve the issue, improve consistency, and reduce scrap rates significantly.
49. What role does simulation software play in metal stamping?
Simulation software plays a vital role in metal stamping by allowing engineers to model the stamping process before actual production. This helps in predicting potential issues such as material flow, springback, and die wear. By using simulation, teams can optimize die design and process parameters, leading to reduced trial-and-error in the physical prototyping stage and saving time and costs.
50. How do you stay updated on industry trends and technologies in metal stamping?
I stay updated on industry trends and technologies by attending conferences, participating in webinars, and subscribing to relevant journals and publications. Networking with other professionals through industry associations also provides insights into best practices and emerging technologies in metal stamping, allowing me to implement innovative solutions in my work.
51. Can you explain the importance of quality control in metal stamping?
Quality control in metal stamping is crucial to ensure that the final products meet specifications and customer expectations. Implementing rigorous quality control measures, such as regular inspections, testing of raw materials, and monitoring production processes, helps identify defects early. This not only reduces waste and rework but also enhances customer satisfaction and trust in the brand.
52. What advanced technologies do you see impacting metal stamping in the future?
- Automation and Robotics: Increasing efficiency and precision in stamping processes.
- 3D Printing: Offering new possibilities for tooling and prototyping.
- Smart Manufacturing: Utilizing IoT for real-time monitoring and data analytics to optimize processes.
These technologies are expected to significantly enhance productivity and reduce costs in the metal stamping industry.
53. How do you manage supply chain challenges in metal stamping?
Managing supply chain challenges involves establishing strong relationships with suppliers, diversifying the supplier base, and implementing just-in-time (JIT) inventory practices. Regular communication with suppliers ensures timely delivery of materials, while JIT helps minimize inventory costs. Additionally, contingency planning for unexpected disruptions is crucial for maintaining production continuity.
54. What methods do you use to improve employee engagement in a metal stamping environment?
- Training and Development: Offering continuous learning opportunities to enhance skills.
- Recognition Programs: Implementing systems to recognize and reward outstanding performance.
- Open Communication: Fostering an environment where employees feel comfortable sharing ideas and concerns.
These methods contribute to a motivated workforce, ultimately leading to improved productivity and quality in metal stamping operations.
These questions are designed for experienced professionals in the metal stamping industry and focus on advanced concepts related to optimization, design patterns, and leadership in the field.
56. How do you optimize the metal stamping process for efficiency and quality?
To optimize the metal stamping process, consider the following key strategies:
- Tool Design: Ensure that tooling is designed for longevity and precision, reducing downtime and rework.
- Material Selection: Choose the right materials that offer durability and are compatible with the stamping process to minimize defects.
- Process Parameters: Adjust parameters such as speed, pressure, and temperature to match the specific requirements of the material and design.
- Automation: Implement automation in the feeding and transfer systems to enhance speed and reduce manual errors.
- Regular Maintenance: Schedule routine maintenance of machines to prevent breakdowns and ensure optimal performance.
By focusing on these areas, manufacturers can significantly enhance both the efficiency and quality of their metal stamping processes.
57. What design patterns do you find most effective in managing complex metal stamping projects?
In managing complex metal stamping projects, several design patterns can be particularly effective:
- Modular Design: Break down the project into smaller, manageable modules that can be developed and tested independently, facilitating easier troubleshooting and modifications.
- Iterative Development: Use an iterative approach to allow for continuous feedback and improvements throughout the project lifecycle, ensuring that the final product meets specifications.
- Standardization: Implement standard processes and components to streamline manufacturing and reduce variability, which enhances predictability in production.
- Lean Manufacturing: Adopt lean principles to eliminate waste and improve efficiency by continuously assessing and optimizing the workflow.
These patterns not only enhance project management but also improve collaboration among teams, leading to more successful outcomes in metal stamping projects.
How to Prepare for Your Metal stamping Interview
Preparing for a metal stamping interview requires a blend of technical knowledge and practical experience. Understanding the processes, tools, and industry standards will help you demonstrate your expertise and suitability for the role effectively.
- Familiarize yourself with metal stamping processes, including progressive, transfer, and deep drawing. Understand the techniques used and the advantages of each type, as well as common applications in various industries, to showcase your knowledge effectively during the interview.
- Review the types of materials commonly used in metal stamping, such as aluminum, steel, and copper. Understand their properties and how they affect the stamping process. Be prepared to discuss material selection based on project requirements and characteristics.
- Brush up on your knowledge of tooling used in metal stamping, including dies, punches, and fixtures. Be ready to discuss how to maintain and troubleshoot these tools, as well as your experience with design and fabrication of custom tooling.
- Gain a solid understanding of quality control measures in metal stamping. Familiarize yourself with inspection techniques, such as visual inspections and the use of calipers and gauges. Be prepared to discuss how you have ensured product quality in previous roles.
- Research industry standards and regulations related to metal stamping, such as ISO 9001 and safety protocols. Demonstrating awareness of compliance and quality management systems will show your commitment to industry best practices and workplace safety.
- Prepare examples from your past experience that demonstrate your problem-solving skills in metal stamping. Think about challenges you faced, how you approached them, and the outcomes. This will help illustrate your practical knowledge and adaptability.
- Practice common interview questions related to metal stamping, such as those about process optimization, cost reduction, and teamwork. Articulating your thoughts and experiences clearly will help you communicate your qualifications effectively and confidently during the interview.
Common Metal stamping Interview Mistakes to Avoid
When interviewing for a metal stamping position, it’s essential to present yourself effectively and avoid common pitfalls. Understanding these mistakes can significantly improve your chances of impressing the interviewer and landing the job.
- Inadequate Knowledge of Metal Stamping Processes: Failing to demonstrate an understanding of processes like die making, stamping techniques, and material properties can signal a lack of preparation and industry knowledge.
- Neglecting Safety Protocols: Not discussing safety measures and protocols in metal stamping can raise red flags for employers who prioritize a safe working environment and compliance with regulations.
- Weak Problem-Solving Skills: Metal stamping often involves troubleshooting. Not providing examples of how you’ve approached and solved problems can indicate a lack of critical thinking and adaptability.
- Ignoring Team Collaboration: Metal stamping is typically a team effort. Failing to highlight your ability to work collaboratively can suggest you’re not a team player, which is essential in a manufacturing setting.
- Not Asking Questions: An absence of questions about the company or role can imply disinterest. Asking insightful questions demonstrates your enthusiasm and helps you assess if the job aligns with your career goals.
- Poor Communication Skills: Metal stamping roles often require clear communication, especially in troubleshooting and team settings. Struggling to articulate your thoughts can undermine your candidacy.
- Failure to Showcase Relevant Experience: Not relating past experiences to the metal stamping role can make it hard for interviewers to see your suitability for the position, even if you have relevant skills.
- Being Unfamiliar with Tools and Machinery: Lack of knowledge about tools like presses, dies, and CNC machines could suggest you’re not well-versed in the essentials of metal stamping operations.
Key Takeaways for Metal stamping Interview Success
- Prepare a strong resume using an AI resume builder to highlight relevant skills and experiences that align with metal stamping roles. Tailor your resume to match the job description.
- Utilize professional resume templates to ensure your resume is well-structured and visually appealing. A clean layout can make a significant difference in capturing the interviewer’s attention.
- Showcase your experience effectively by referring to resume examples that demonstrate accomplishments in metal stamping or related fields. This will help illustrate your capabilities during the interview.
- Don’t overlook the importance of cover letters; they provide an opportunity to express your passion for metal stamping and explain how your skills make you a great fit for the company.
- Engage in mock interview practice to build confidence and improve your ability to answer technical and behavioral questions related to metal stamping roles. This preparation will enhance your performance.
Frequently Asked Questions
1. How long does a typical Metal stamping interview last?
A typical metal stamping interview can last anywhere from 30 minutes to an hour. The duration often depends on the complexity of the position and the number of interviewers involved. Expect a mix of technical questions and behavioral assessments to gauge your skills and fit within the company culture. Be prepared to discuss your experience and knowledge about metal stamping processes, materials, and machinery used in the industry.
2. What should I wear to a Metal stamping interview?
For a metal stamping interview, it’s best to dress in business casual attire. This typically includes dress pants and a collared shirt for men, and slacks or a knee-length skirt with a blouse for women. Avoid overly casual clothing, such as jeans or sneakers, as they may give the impression of a lack of professionalism. Being well-groomed and presentable can leave a positive impression on your potential employer.
3. How many rounds of interviews are typical for a Metal stamping position?
For a metal stamping position, candidates can typically expect two to three rounds of interviews. The first round is often a phone or video interview focusing on general qualifications and experience. Subsequent rounds may involve in-person interviews with technical assessments or practical evaluations. Some companies might include a final round with management to assess cultural fit and discuss the role in more detail.
4. Should I send a thank-you note after my Metal stamping interview?
Yes, sending a thank-you note after your metal stamping interview is highly recommended. It shows your appreciation for the interviewer’s time and reinforces your interest in the position. A brief email expressing gratitude, highlighting a key point from the interview, and reiterating your enthusiasm for the role can leave a lasting positive impression. Aim to send this note within 24 hours of the interview to ensure it is timely and relevant.